Make the perfect cut at the fastest line speed possible. This is next generation technology, backed by five generations of traditional Jarvis craftsmanship. Capable of increasing your yield at throughputs up to 900 head per hour per machine. And already setting a new standard in accuracy, hygiene, and reliability under the most demanding conditions. Welcome to the JLR-900. The fastest pork splitting robot ever made.
Up to 900 head per hour per machine. Configurable to outpace the fastest line speed.
We design, manufacture, and test each JLR-900 to outperform anything else. We’ve built this robot for customers who need the most extreme processing power, never sacrificing on cut quality. Proven to increase your yield at throughputs up to 900 head per hour per machine. And faster than any other robot out there.
JLR-900
Current Generation Linear Robot
Past Generation Linear Robot
Past Generation Industrial 6-Axis Robot
Hand Saw
Faster. More accurate. Made with way fewer parts. The JLR-900 completely reimagines the pork splitting process to maximize your speed and increase your yield. No more expensive ball screws. No more wasteful air cylinders. No more complicated sub-systems. Just record-setting throughput. With fewer and higher-quality food-grade components packed inside fully automated cutting and stabilizing modules, the JLR-900 delivers better results without stopping for repairs. So you can increase uptime and lower your total cost of ownership.
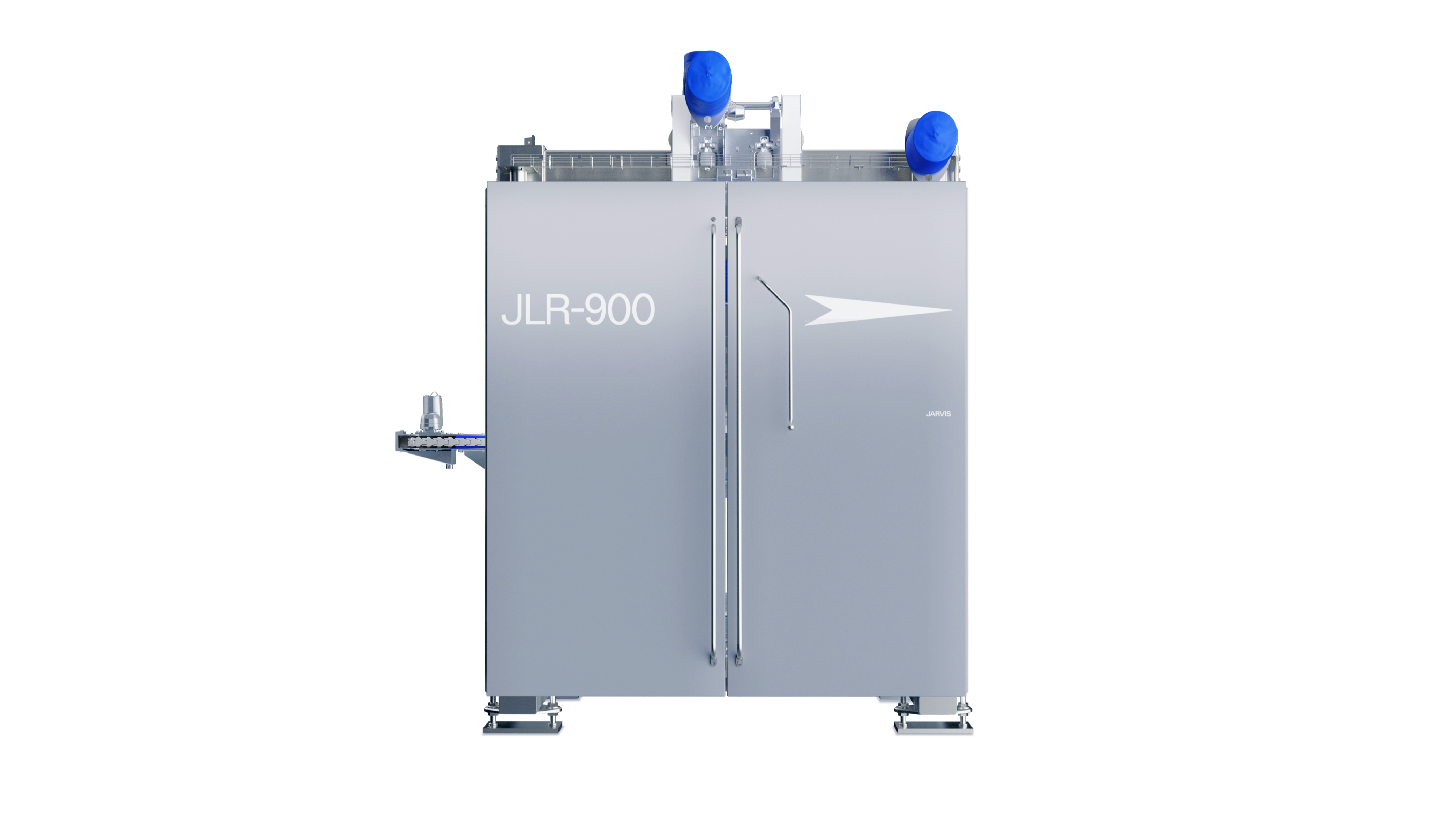
A three-stage stabilizing module.
For perfect cut after perfect cut. After perfect cut.
To make the perfect cut, you need total control. Previous linear robots used a complex, air cylinder-driven system to operate the stabilizing module, which inhibited complete alignment of the carcass before a cut. The new stabilizing module runs on a z-axis servo motor and works in three stages to position the carcass against the saw with more precision than any other of its kind. After the carcass length is measured with a light curtain, the in-feed conveyor outside the machine matches the speed of the line to smoothly transition the carcass into the JLR-900. Large rollers extend on a servo motor-powered arm, preventing any motion of the carcass, while carefully moving it towards the saw side of the machine, as leg spreaders hold the hocks in place and the body grabber secures the lower half of the carcass.
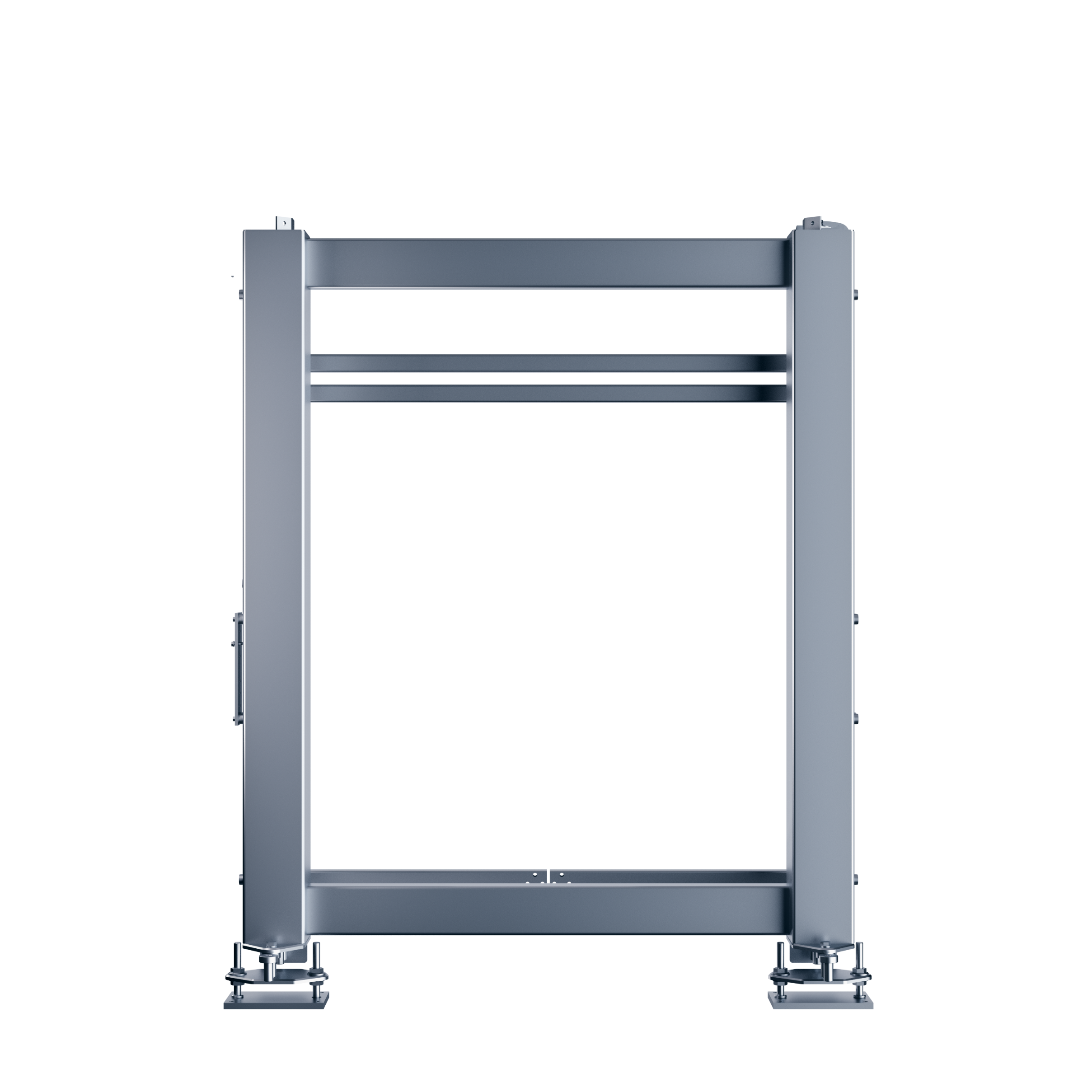
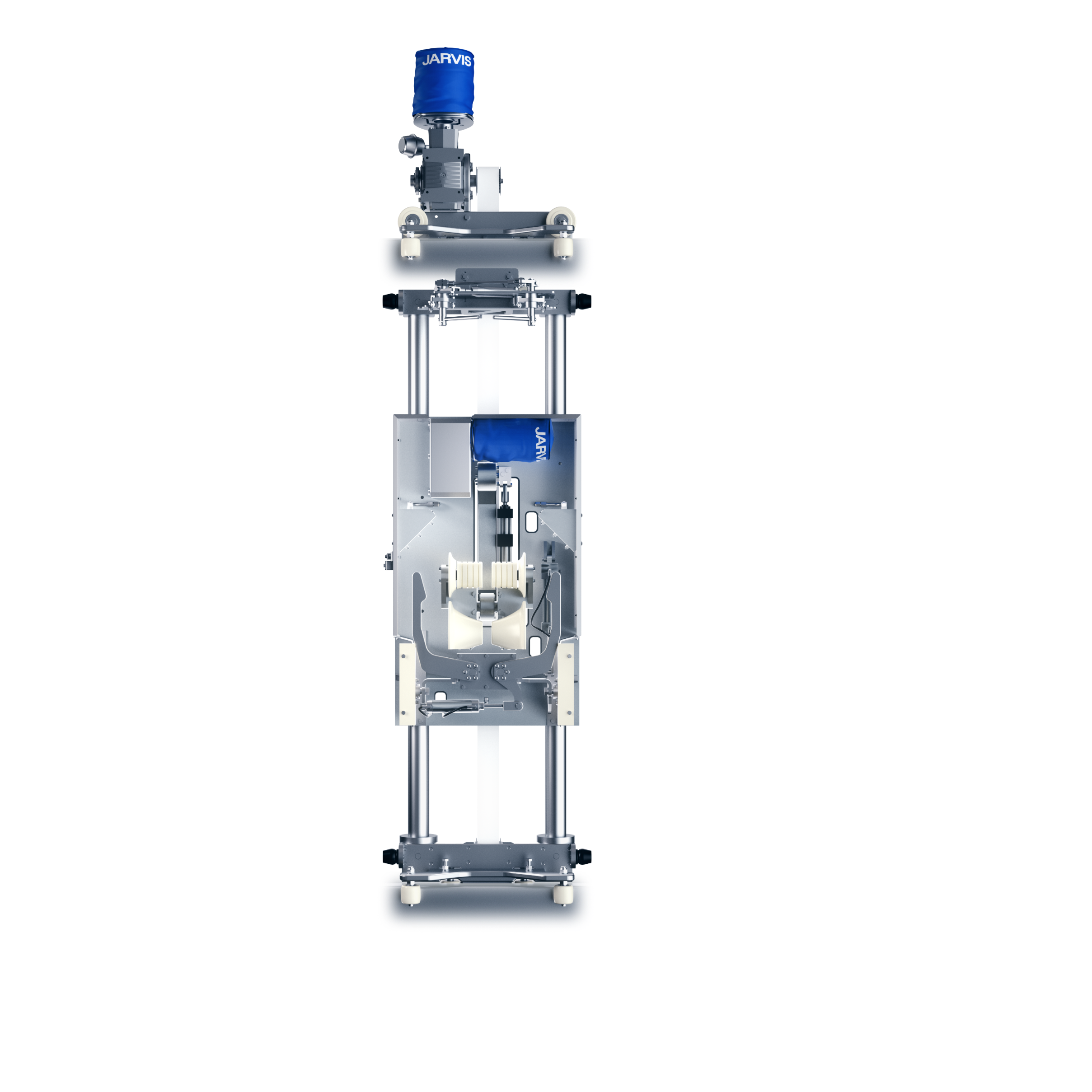
- ALeg Spreaders
- BPlastic Rollers
- CBody Grabber
A set of pneumatically-powered leg spreaders sit on top of the stabilizing module to assist in aligning the carcass. Running on newly designed track wheels, the leg spreaders open and close to hold the animal’s hocks in place — adding yet another layer of stability and control to the process. Each element of this system is designed to reduce the micro-movements of the carcass once inside the machine.
Most plastic rollers in linear splitting robots extend on an air-cylinder powered arm with uncontrolled movement on the z-axis. But this type of system hinders complete alignment of the rollers against the random shapes and sizes of some carcasses. The JLR-900’s rollers are made from food-grade plastic and utilize a servo-motor controlled arm, allowing them to extend and retract to any depth for total control of the carcass. And with no need for an air-cylinder to operate the system, the new stabilizing module is even easier to maintain.
The body grabber is laser cut from aluminum, then is hand contoured for the best ergonomic fit around the varying topography of each carcass. During a cycle, the body grabber folds down from the stabilizing module and opens up to receive the carcass into the machine. As the rollers move the carcass towards the spine guide before a cut, the body grabber gently closes around the lower half of the animal.
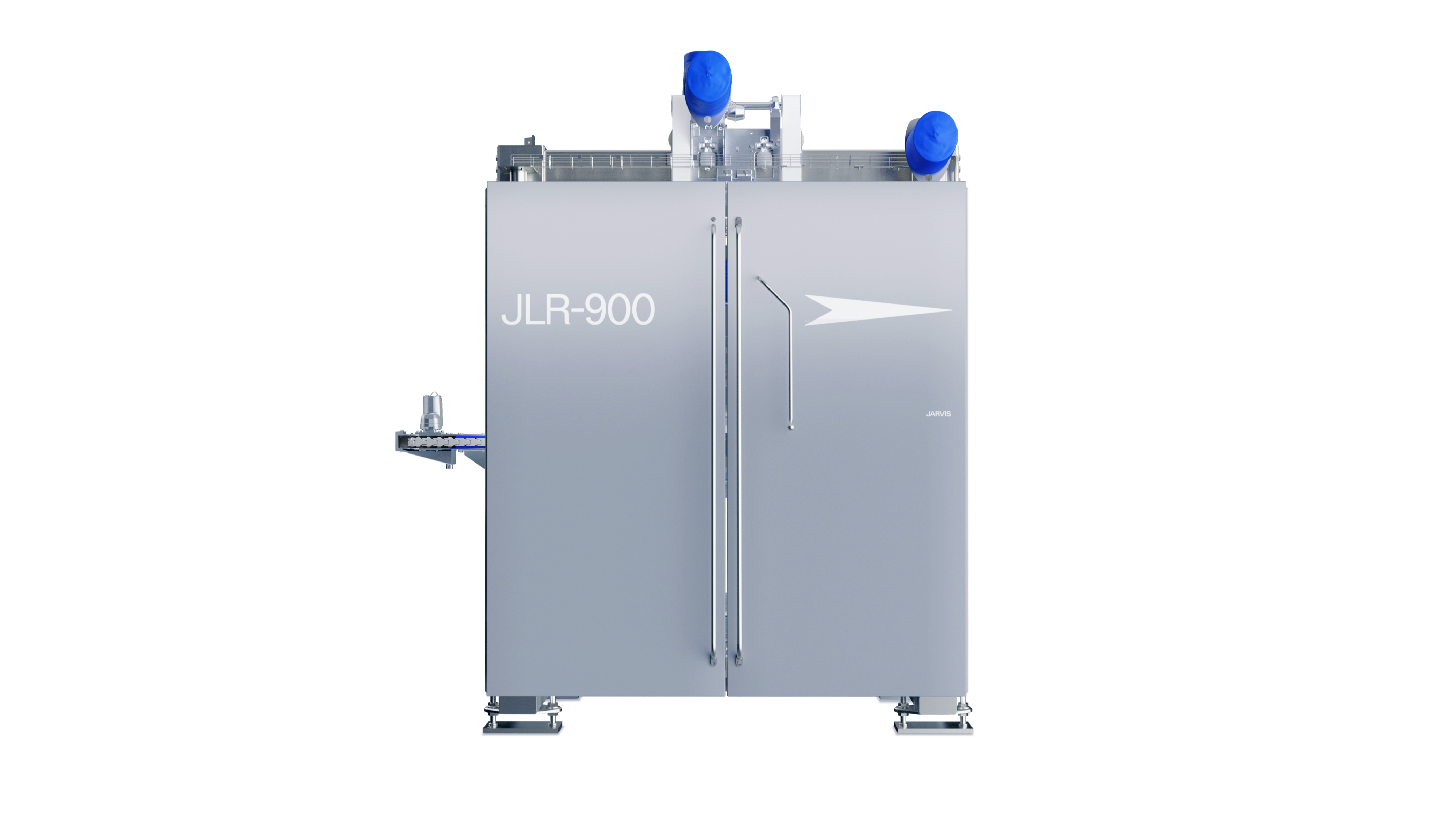
The iconic Jarvis arrow points to the future; to the continued progression of our products, our planet and the communities we serve. For over 100 years, we’ve been powering innovation for a healthier world. Affixed to the stainless-steel sliding doors of the JLR-900, our new logotype and symbol reflect the intense passion, responsibility, and sense of learning with which we approach the problems we solve. You can learn more about our evolved identity here. But for now, keep exploring the fastest pork splitting robot ever made.
With the carcass aligned inside the machine, the saw cuts from top to bottom, supported by food-grade Kevlar timing belts and ultra-long-life bushings on y-axis guides. We purposefully designed everything about the JLR-900 to make operation and maintenance a breeze. A super lightweight, modular saw frame for easy disassembly. Jarvis circular blades, and automatic self-sanitizing and swarf control systems.
The industry standard saw module.
Setting a new standard.
The Jarvis linear saw module is already used on most automated splitters. And there’s a reason for that. Our modular skeleton frame surrounds the saw head and is extremely easy to take apart. This decreases the weight of the assembly, turning maintenance into a quick, one-man job. Now in its third generation, the JLR-900’s saw module is specifically engineered to cut your downtime in half. The spine guide is fixed in place to prevent the need for another tilt air cylinder to lower air requirements for operation. Radiused edges within the machine stop the build-up of bone dust and water. And swarf control and self-sanitizing systems automatically clean the machine after every cut. All parts of the JLR-900 work in synchronicity, so you won’t need to slow down.
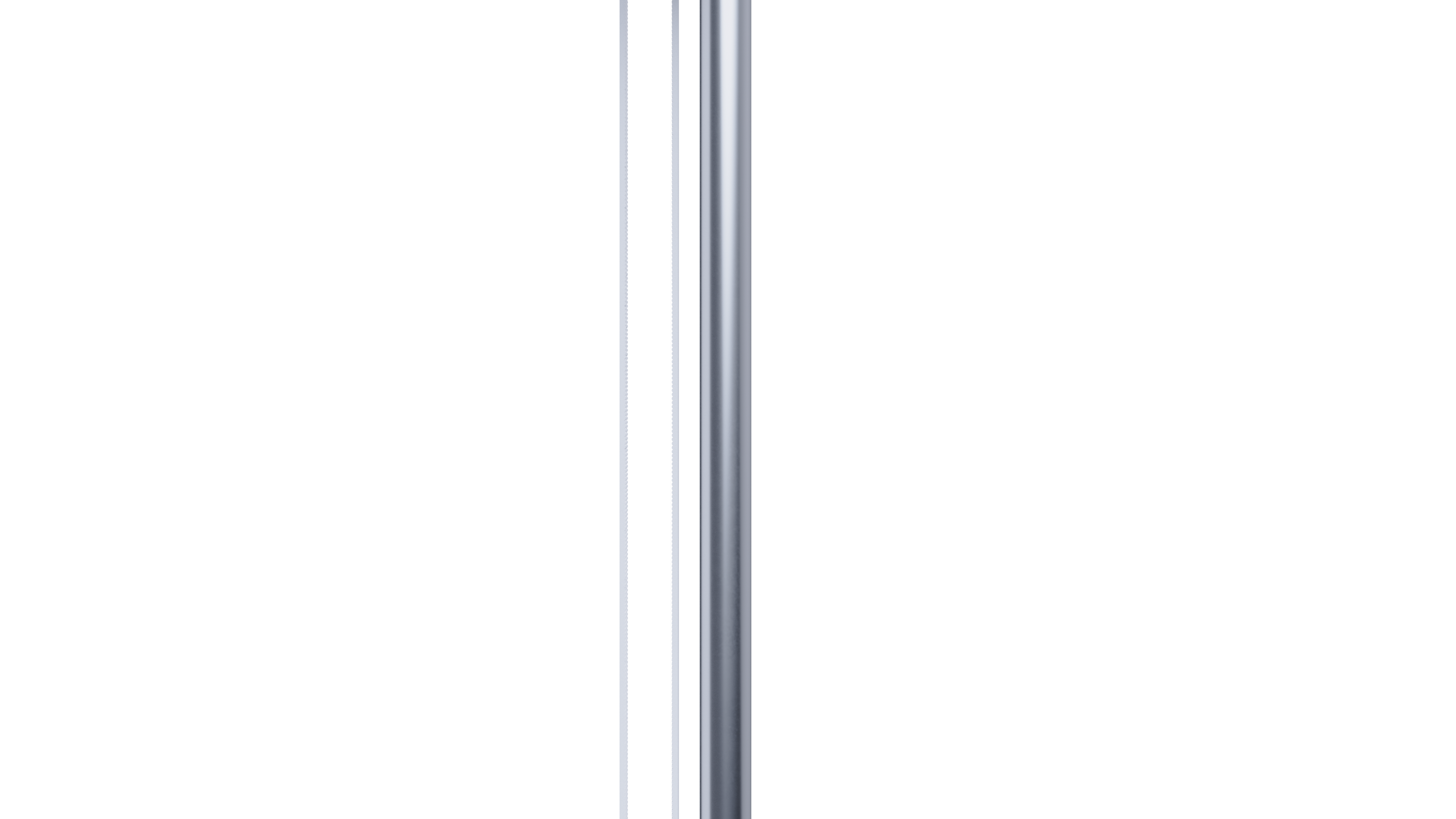
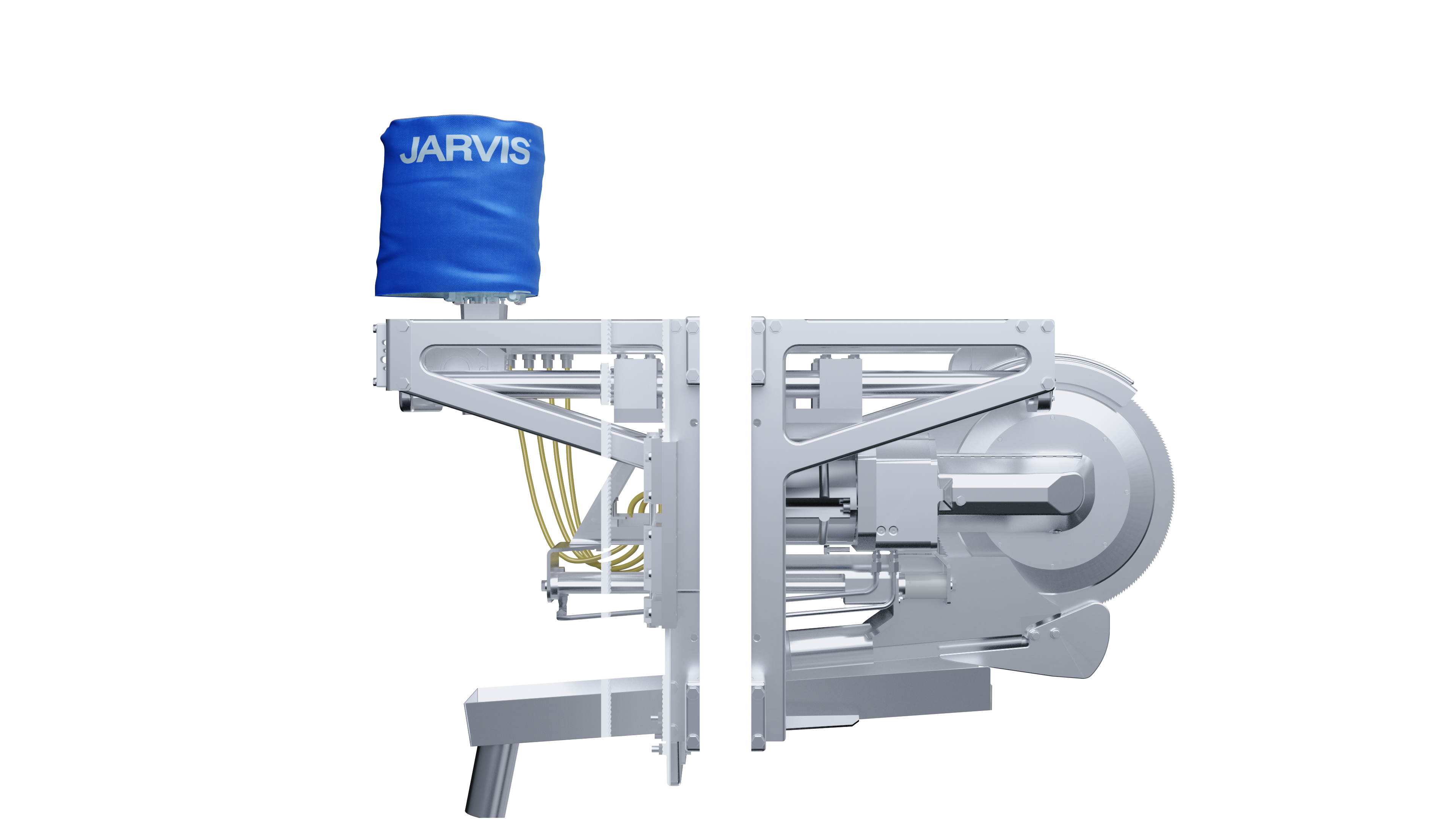

- AJarvis Circular Blade
- BLong-Life Bushings
- CRadiused Edges
Jarvis circular blades undergo a unique manufacturing process where they’re carefully treated for extreme cutting performance. The JLR-900 uses a 465-millimeter diameter blade — ground from the highest quality stainless steel. Learn more about our blade reconditioning program here. We’ll keep you constantly stocked with professionally-sharpened blades, so you can run around the clock without worrying about repairs.
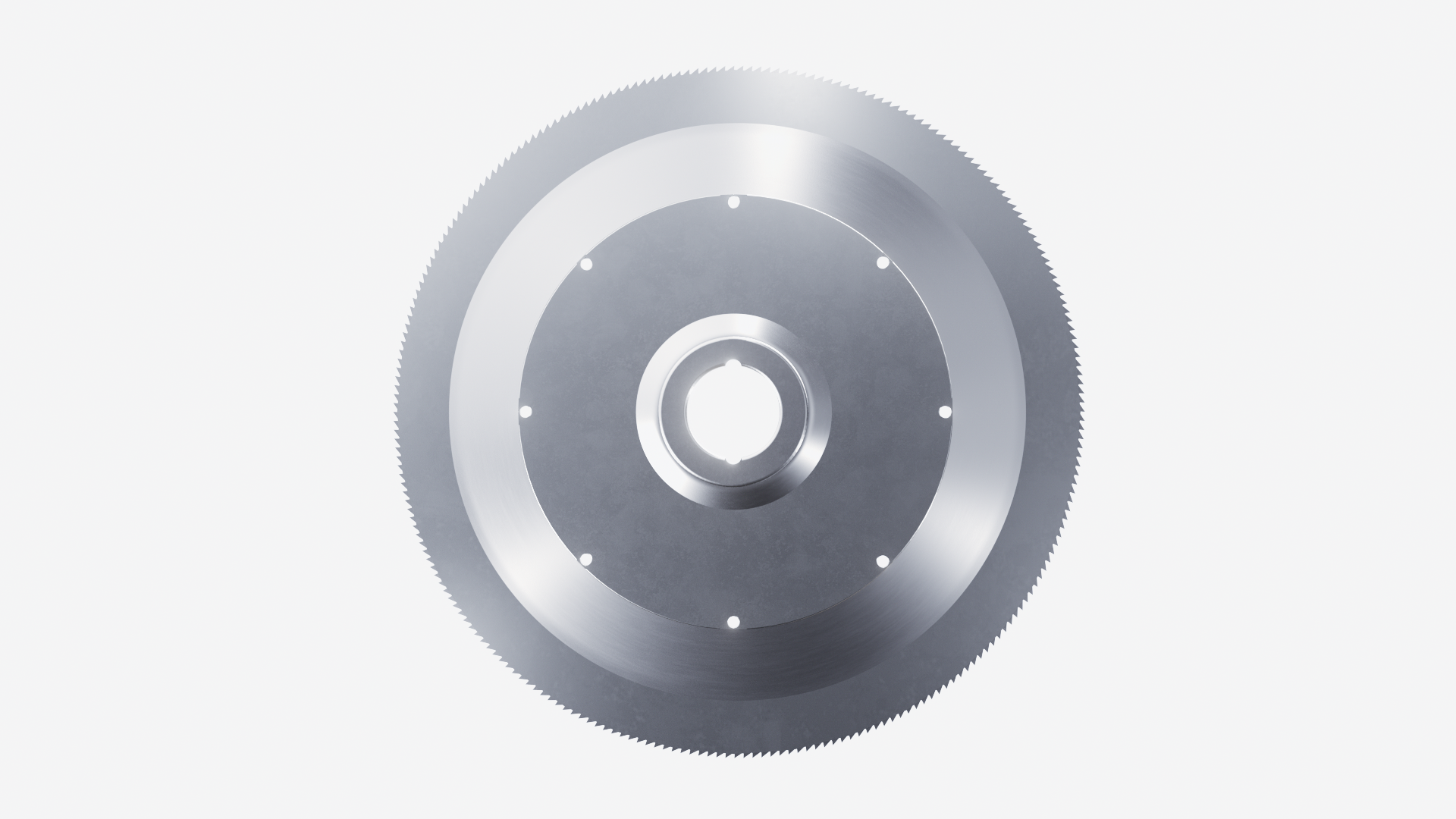
The JLR-900’s stabilizing and saw modules move up and down lightweight y-axis guides with the help of durable ceramo-plastic bushings. This new full bushing design uses the latest in material technology and replaces horseshoe bushings to prevent uneven wear and reduce your maintenance load.
We’ve designed each bracket and block down to the finest details to uphold the highest standard in cleanliness. The JLR-900 is manufactured with intentionally radiused edges in key areas that are exposed to bone dust and water throughout a cut cycle. These rounded corners prevent the collection of any debris or liquid leftover from sanitizing washes, allowing you to slash clean-up time to 10 minutes, and to deliver the most hygienic final product.
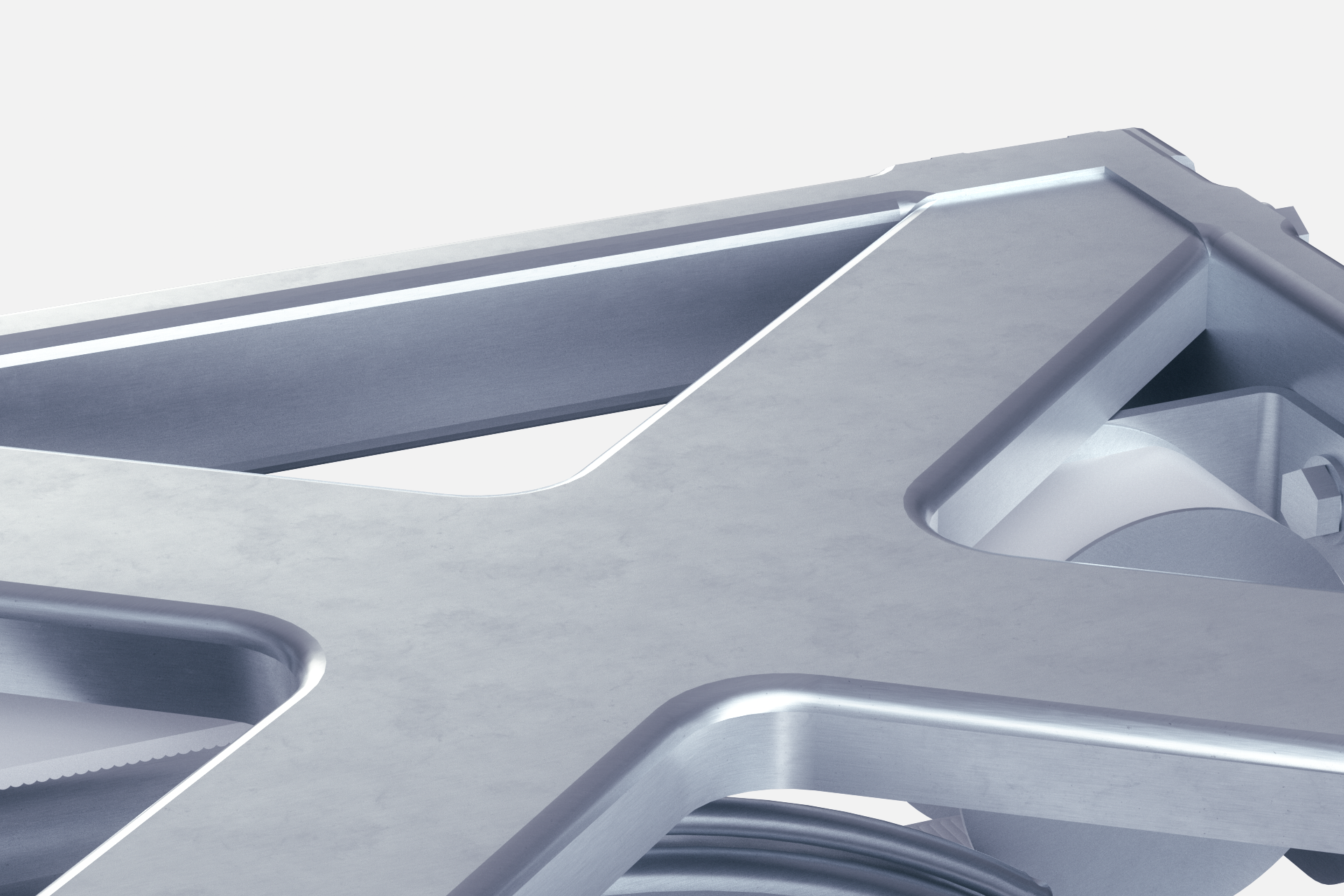
Maintenance made easy.
The frequency and time it takes for repairs can make or break your total cost of ownership. When developing the JLR-900, we didn’t just reach a new level in processing power and cut quality — we also created the most commercially viable robot. Previous saw modules required testing and maintenance of the oil sump lubrication system used to keep the gearbox running. So we replaced that with a robust spiral head reduction with grease, eliminating pump failures and oil testing completely. And by combining custom stainless-steel components with our innovative saw head design, we successfully cut down the need for preventative maintenance from daily to once every three months.
Current Generation Linear Robot
Cleans itself,
so you don’t have to.
Excellent hygiene is critical to the perfect cut. The JLR-900 uses state-of-the-art self-sanitizing and swarf control systems located on both the saw and stabilizing modules to eliminate the need for more human operators. Four sets of high-pressure jets near the saw head and rollers automatically rinse internal components during and after each cut cycle.
Current Generation Linear Robot
Past Generation Linear Robot
by 2 people
A deeper clean.
With 50% less water.
Low flow laminar wetting tubes above the saw transmission coat the module in a protective liquid barrier and jets rinse the stabilizing module and blade after every cycle as bone dust and debris are funneled away from the carcass. Stainless steel pipes recycle the motor cooling water that keeps the system running without failure to jets on either side of the assembly. This closed-loop sanitizing system uses approximately half the amount of water as past generation machines, saving you more resources and lowering your total cost of ownership.
Current Generation Linear Robot
Past Generation Linear Robot
Run for longer. Faster. Cooler.
Water travels through enclosed pipes into the 15 HP saw motor, preventing the machine from overheating while operating at incredibly fast throughputs. As the JLR-900 runs through a cut cycle, cold water pumps into a special casing around the motor, then is heated up and funneled back to the sanitizing system for the most hygienic hot rinse of the saw and stabilizing modules.
Over 12 meters of custom bent stainless-steel pipes.
We knew that building the most reliable robot meant taking no short-cuts along the way. The JLR-900 is a powerful blend of advanced automated technology and traditional Jarvis craftsmanship. All of the systems inside the JLR-900 are connected by custom stainless-steel pipes that are bent by hand in our factory, instead of outfitting our modules with the same plastic components used on competitor machines. We put the highest quality food-grade components through precision manufacturing processes, so you can withstand continued operation at the fastest line speed possible.
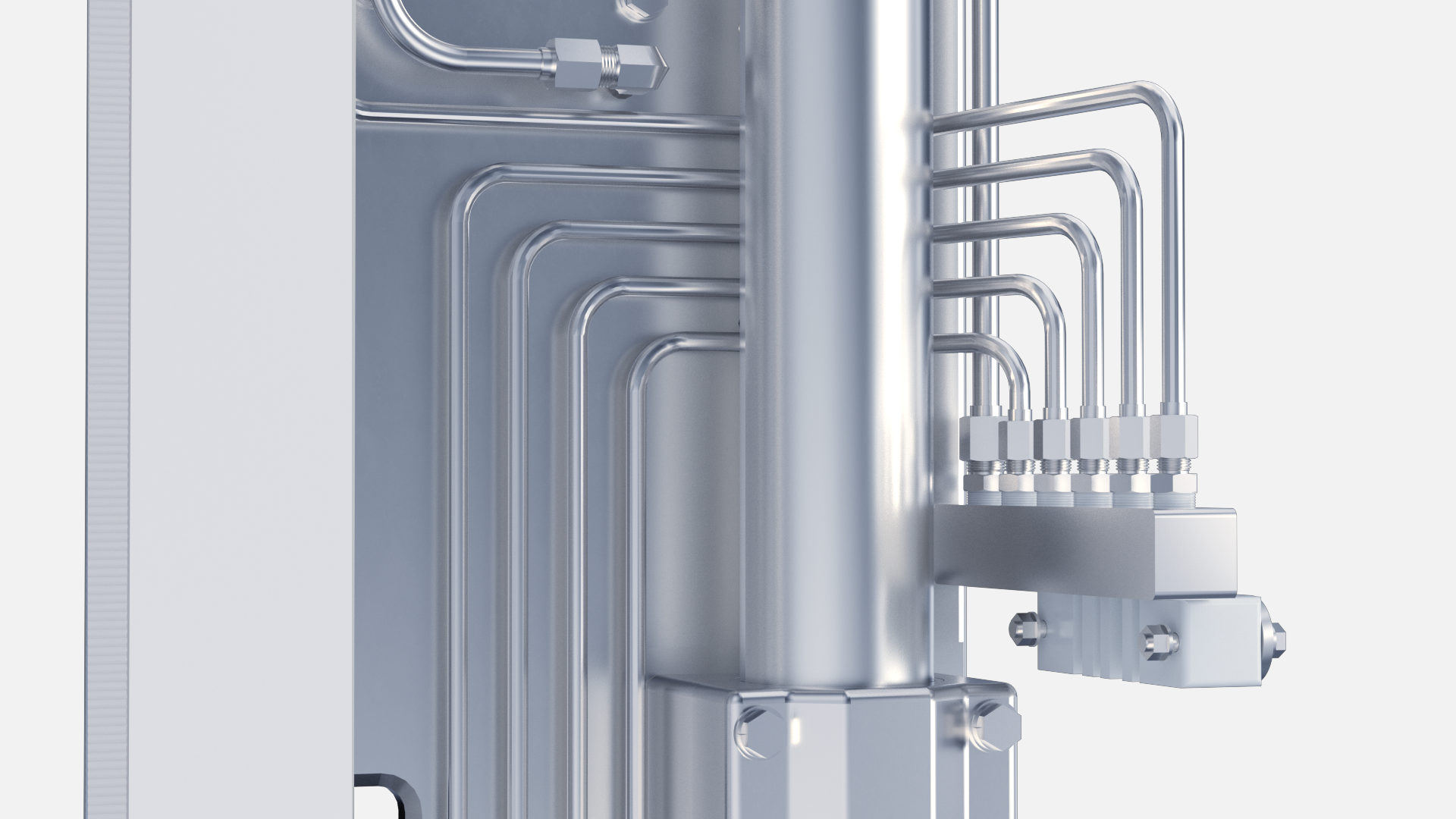
More power to the operator.
The JLR-900 is controlled by a durable 14” IP67 Siemens HMI mounted in a NEMA 4X rated 304 stainless steel enclosure and features a completely redesigned interface with operator, engineer, and maintenance specific screens programmed for seamless setup and operation. Filled with run-time statistics like cycle rate, cycle times, saw speed, and chain speed — plus machine diagnostics including active alarms and alarms log — the Jarvis HMI is a powerfully intuitive control center with everything you need in one place.